by Laura Cordoba, email laucordobarios@vt.edu
The wood market share includes environmentally friendly products such as thermally-modified (TM) wood. Wood products companies are working hard to create new products and to improve their production processes to satisfy their clients, meet financial goals, and to reduce their environmental footprint.
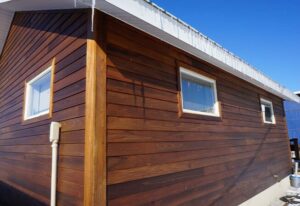
Wood is commonly known for being a versatile renewable resource and in general is a non-toxic material. As a natural product, wood must go through a value-added transformation to acquire the desired functionality. Thermal modification is a known process for this transformation, and it has been recently adopted by industries around the United States. This wood modification process is attractive for the market because creates a price competitive product, with great stability, increase decay resistance, and free of chemicals (Aro et al, 2014).
Thermally-modified (TM) wood has been available since the early 1990s in Europe, where it was developed as a substitute product to tropical hardwood lumber. TM wood is a product that is relatively new in the U.S. Therefore; consumers such as architects, engineers, building contractors, and end consumers are still hesitant about its potential and use (Wardell 2015). The fact that this kind of wood modification technique is new in the US provides chances to find improvements for the product and the process itself.
Lean thinking provides an opportunity to identify current problems that are affecting the manufacturing process of TM wood. Lean thinking is a business model that help managers to identify waste in the value stream of manufacturing, supply chain and services processes. Besides the presence of waste, long lead times, and high manufacturing costs are also part of the main concerns present in the manufacturing of TM wood. These issues could make a negative impact on the efficiency and effectiveness of the manufacturing process.
The first activity in the implementation of Lean Thinking in the production TM wood is to understand the production process. A mapping of the process is the first step following by the developing of efficiency and effectiveness metrics such as production rates, inventory levels, production costs, and lead times metrics. The second activity is to identify improvement opportunities and non-value activities on the manufacturing process of TM wood. The final activity is to design an improved production process that can help to solve the current issues. Lean thinking offers a variety of tools such as visual control, standardization of procedures, 5S, and plant layout that can be used to solve the issues and improve the current process.
A project like this requires to set up meetings, interviews, and walk-throughs to be able to map and obtain the required performance metrics to understand the current state of the process. Analysis of production data is also critical. The mapping of the process is conducted through value stream map (VSM). An Ishikawa diagram is also used to help understand the causes for the current issues. The future state or solution is also displayed on a new VMS culled the future VSM. In addition and economic analysis is conducted to tie the potential solutions to financial aspects.
References
- Aro, M., Bradshaw, B., and Donahue, P. 2014. Mechanical and Physical Properties of Thermally Modified Plywood and Oriented Strand Board Panels. Forest Products Journal. 64(7/8):281-289.
- Wardell, C. 2015. Thermally modified decking. Professional Deck Builder. June. pp:42-44