by Gaurav Kakkar, Virginia Tech MS student. kakkarg@vt.edu
Introduction
Traditional construction process involves shipping of raw materials to the construction site. The contractor/sub-contractors would then use on-site workers to process and use them in building. Since most of the work is done on site, majority (up to 90%) of the total cost is incurred on the actual construction site (Somerville, 1999). This means majority of the project is done in open, uncontrolled environment. Instead, Prefabricated construction refers to construction for which 2/3 or more construction process are finished in factory and the main parts of the house, such as walls and floors, are fabricated following certain industry standards. This gives builders an option to build faster assuring safety and quality at lower prices as compared to on-site construction (WoodWorks, 2014). The components are prefabricated in batches and then shipped to site for assembly. The level and nature of prefabrication can vary from project to project.
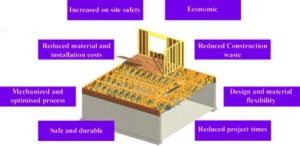
Depending upon the extent of prefabrication, these off-site manufactured systems can vary from just pre-cut and prefabricated components to panelized leading up to fully advanced modular systems. These are also called building systems (Na, 2015). Factory manufactured components in these systems replace some of the on-site labor built structures. The process is mainly feasible in repetitive components of house like, walls, floors, doors and windows etc. which when assembled easily on site can be very effective in saving time.
Evolution of Building Systems in Wood construction
Home manufacturers provide builders with a different product types with varied degree of prefabrication. These houses in the United States are manufactured strictly according to the concerned state wide building codes. This report does not include the manufactured/mobile housing which is regulated under HUD codes.
Prefabricated systems
This is the most basic type of off-site factory manufacturing of building components. This system evolved with the wide spread of lumber mills which started to supply processed dimensional lumber to the builders. All the cutting, drying and processing is done in a central location and then supplied to the builder on the construction site. The builder would then use these to make walls, floors or roof systems. This system further gained popularity with the development of engineered wood products like Structural Insulated Panels (SIP), trusses, I-joists (WoodWorks, 2014) etc. which required mechanized manufacturing by skilled labor and cannot be done easily on the construction site. The manufacturers now make them in many configurations and types giving builders a wide variety to select from to fulfill the design and regulatory requirements.
Panelized systems
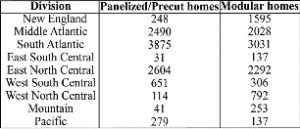
With further development in factory manufacturing of wood products, the wood products industry moved to assembling the prefabricated products into larger panels or complete assemblies. These panelized systems can be engineered according to construction design. Use of computer added design further helps the manufacturers to manufacture exact dimensions quite easily (WoodWorks, 2014). Using panelized systems, complete wall panels, floor and roof systems can be delivered to the site ready for assembly and installation. Some systems come even with plumbing and electric fittings so that factory built systems are not tampered.
Modular systems
This is the most advanced building system in which the entire house is divided into independent modules during the design. These modules are then built in a factory on a production line like any other manufacturing. Controlled environment, skilled labor and use of automation in construction makes this off-site manufacturing very quick as compared to on-site construction. These modules are fitted with all the utility fittings and insulated properly before they leave the facility. Some modules might even come with interior finishing like carpeting, kitchen cabinets and shelves etc. A complete module is transported to the job site where it would be connected and sealed with the rest of the structure to complete the building. This type of the building system has maximum amount of prefabrication ranging up to 95% of the total construction work done off-site. In order to assure sufficient safety and durability, the modules are inspected at factory during construction and on site at the time of installation as well. This method can complete a project in half the time as compared to traditional stick built on-site construction (WoodWorks, 2014).
Adoption of prefab system in the United States.
Prefabrication in residential construction is not a new concept. The first adoption of off-site construction in the United States dates back to mid-1800s (O’Brien, Wakefield, & Beliveau, 2000) but the industry is still to have a widespread acceptance of advanced prefabricated systems. This is supported by 2014 Survey of Construction (Zhao, 2015) which reported that only 10,334 single family panelized/precut home and 10,560 single family modular homes were started in 2014 which also were geographically concentrated in East North central, South and Mid-Atlantic regions of the country. This amounts to 3.2% of the total single family residential construction in 2014. Along with less adoption, the market penetration of off-site construction was observed to be diverse.
Drivers for future growth
The key feature of off-site construction and adoption of factory manufacturing techniques in construction sector is improvement in project schedules. With optimized manufacturing processes, builders can achieve a considerable improvement in time taken to complete a project. Including prefabrication can also reduce construction costs mainly by optimizing material use and reducing waste. There can be substantial improvement in site safety with majority of the work done in the controlled environment of a manufacturing facility. Green and Energy efficient buildings can be constructed in a more efficiently by including prefabrication. Prefabrication in construction can also give builders and architectures a flexibility to use wide range of materials and work without any interruption by inclement weather conditions (McGraw-Hill Construction, 2011). As the industry gain more maturity, these factors In future would further encourage the builders to adopt higher levels of off-site manufacturing in residential construction.
References
McGraw-Hill Construction. (2011). Prefabrication and Modularization: Increasing Prductivity in the Construction Industry. Bedford, MA: McGraw-Hill Construction.
Na, Z. (2015, October 1). System Built Single Family Homes in 2014. Retrieved February 10, 2016, from Housingeconomics: http://www.nahbclassic.org/generic.aspx?sectionID=734&genericContentID=247892&channelID=311
O’Brien, M., Wakefield, R., & Beliveau, Y. (2000, July). Industrializing the residential construction site. Retrieved from HUD User: http://www.huduser.org/portal/publications/manufhsg
Somerville, C. T. (1999). Residential Construction Costs and the Supply of New Housing: Endogeneity and Bias in Construction Cost Index. The Journal of Real Estate Finance and Economics, 18(1), 23-62.
WoodWorks. (2014). Putting the Pieces Together. WoodWorks.
Zhao, N. (2015). System-built single family homes in 2014: Special Study for housing economics. Retrieved from http://www.nahbclassic.org/generic.aspx?sectionID=734&genericContentID=247892&channelID=311