Context diagram is used to show the interaction between a system and its important external factors (Kossiakoff and Sweet 2003). We use this method to analyze the system boundary of the engineering process in a wooden furniture firm. From Figure 1, we could identify two suppliers in the current engineering design system – product development and production. In this case, product development leads the following tasks:
Fabricate original product samples and ship to customers for confirmation
Confirm the design changes and acquire product original drawings from customer
Compile engineering and fabrication specifications for each product collections and handover to engineering for generating production documents
Deliver the customer-confirmed color boards to facilitate production
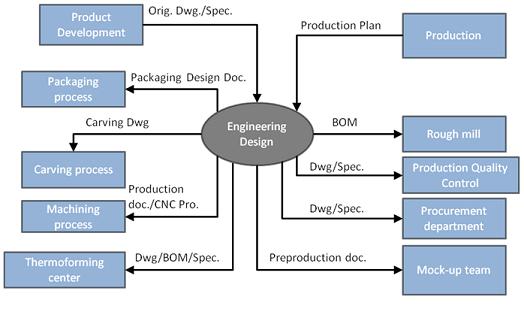
The other supplier, the production department, needs to make sure that they can deliver the updated production plan to the engineering department on a timely basis because this schedule is the foundation to set up the engineering plan. As engineering always takes up a great portion of production lead time, an accurate engineering plan could always ensure the on-time delivery of products. According to our survey results in a furniture company, it shows the engineering accounts for 21%-40% of production lead time.
In the customer perspective, engineering provides service for a number of manufacturing processes:
Rough mill: since rough mill is responsible for processing the raw material into treated material that prepared for machining process. So engineering provide bills of material to the rough mill by providing the following information:
- The quantity of materials needs to be prepared
- The rough and net dimension of each pre-machining component
- The number of each component
- The board dimension for panel gluing or brick stacking
Machining process: engineering needs to provide machining process with a number of essentials:
- Fabrication drawings for making components
- Assembly drawings for subassembly and final assembly of products
- Profile drawings for verifying the precision of component fabrication accuracy
- Programs for CNC manufacturing
- Bills of material for checking component dimension and part number
- Bills of material (BOM) to require hardware and accessories for assembly
Production quality control: engineering provides essential assembly drawings, instructions, and specification to help quality control ensure the quality of products during production proces
Thermoforming center: in general, this process has three functions:
- Provide wood-based panel to production plants. In this case, the engineering needs to prepare bills of material for thermoforming process that indicates the amount and dimension of the material in demand.
- Fabricate fancy panel for production. In this case, the engineering provides them with veneer drawings for parqueting veneer on face panels.
- Fabricate plywood panel. In this case, the engineering provides drawings for verifying the shape of fabricating panels. Also, the CNC engineers are responsible for providing programs for the die fabrication.
Carving process: engineering provides carving drawings to the carving process
Packaging process: packaging engineer takes in charge of generating packaging documents for packaging process. A packaging document typically includes the drawings, bills of material, and instruction of packing up a specific furniture product
Procurement department: engineering provides drawings and specification for the new material and tooling purchase
Mock-up team: this team taking in charge of implementing preproduction and it is a very necessary step before mass production. It has the full function in mass production. Thus engineering not only provides preproduction documents for this process, but also track the fabrication progress and help to solve problem due to design flaws.
Reference:
Kossiakoff, A., and W. N Sweet. 2003. Systems engineering: principles and practice. Wiley-Interscience.