Introduction
Many furniture manufacturers do not have an efficient engineering process. As a result, problems are usually reflected as longer processing times for drawings that leads to production delays, high engineering errors rate affecting product quality, and excessive changes, higher costs and excessive waste. Presently, furniture manufacturers are trying to implement effective Lean Thinking methodologies for manufacturing process to reduce cost, improve quality, and shorten lead time in order to increase their competitiveness – This research utilizes value stream mapping (VSM) and simulation methods to implement a lean management application in the engineering process for wood furniture companies.
The application of Lean Thinking
Lean thinking principles encompass systematic approaches both on management level (Keyte & Locher 2004) as well as manufacturing level (Womack & Jones 1996). Lean management helps people to implement lean transformations in supporting processes such as accounting, engineering, customer service, and sales other than manufacturing. Lean Thinking, of course, can perform a lean transformation for a production process such as molding, fabricating, packaging, and finishing.
The role of engineering
Engineering takes into effect at an early stage of product life cycle, bridging the design and manufacturing transforming a design idea into a production reality. Thus, it plays an important role to reduce cost (either product development cost or manufacturing cost), ensure quality, and time-to-market. In Figure 1, we could see that, cost incurred in fixing mistakes increases from early stages to late stages of product life cycle while the amount of control decreases at the same period.
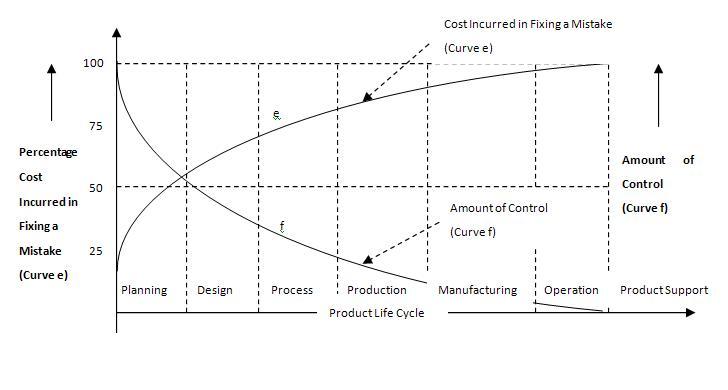
Value stream mapping (VSM)
Value stream mapping (VSM) is a useful lean implementation tool to help people identify both value-added and non-value-added activities in a process and eliminate wastes for process improvement. Figure 2 shows nine types of wastes in a furniture engineering process based on preliminary study. Figure 3 presents a simple furniture engineering process.
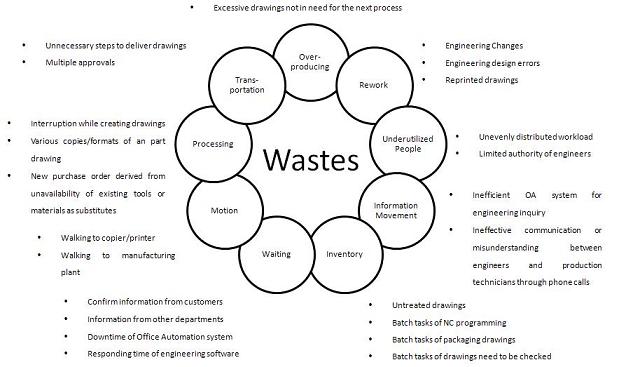
Some furniture engineering processes, such as “create drawings”, always take a long lead time. Some reasons lead to this scenario could be due to the various interruptions to engineers when they create drawings, multiple approvals process, large batch sizes of tasks, or excessive engineering changes.
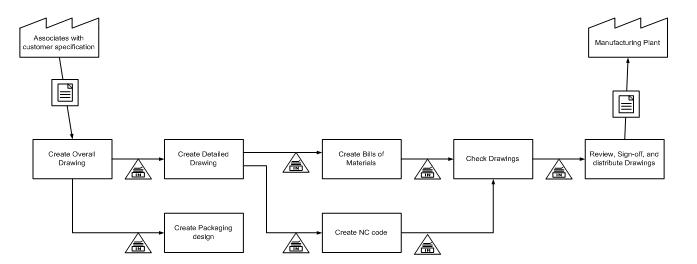
These kinds of activities do not create value toward customer which should be eliminated or improved. Next step, we will focus on precisely measuring each value-added process and non-value-added process by mapping a complete current state VSM of the case study company, and then focus on how to eliminate the wastes in the process by applying appropriate lean tools. Specifically, we will follow Lean Think principles (Womack & Jones 1996) to incorporate the Lean Engineering process:
- “Specification value” – specify the value that defined by the customer, but not by the engineers or any other people within the organization.
- “Identify the value stream” – figure out all the processes involve in delivering engineering documents to internal customers. “Flow” – create continuous value-creating steps flow and reduce batch sizes for a single-task process.
- “Pull” – pull the value from customer. Every process along the engineering value stream should be aligned with customer’s needs and satisfy these needs when it is needed.
- “Pursue Perfection” – lean principles endlessly strive for perfection, avoiding unnecessary waste and errors in the processes and keep implementing continuous improvements.