From November 17-24, 2010 Dr. Henry Quesada and Scott Lyon, graduate research assistant visited 8 forest product importers, 2 non-government organizations, and 2 governmental forestry agencies in Guatemala and El Salvador. The researchers were examining the forest products markets in these countries to identify opportunities for Appalachian forest products companies. The researchers used a structured interview to gain valuable information about the companies and organizations. The objectives were to: (1) identify main competitors of forest product companies in Central American countries; (2) investigate distribution channels of forest products; and (3) investigate local production, demand, and policy of forest products in Central American countries.
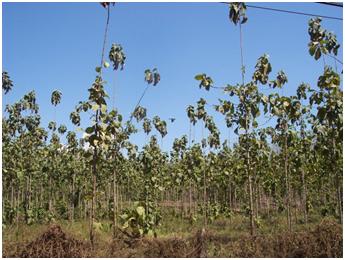
The researchers found that restrictive regulations in these countries may create an opportunity for Appalachian forest products. The Guatemalan government requires permission and payment of taxes before harvesting, causes a decrease of timber harvested. In El Salvador, beginning in 2011 the government will be checking for legality of the wood to prevent illegal harvesting of timber. A permit must accompany the wood product through the harvesting and manufacturing process, which may cause some companies to look elsewhere for raw material. Currently trees are harvested from agroforestry sites such as coffee plantations. These trees are small in diameter and low quality. There is only a small amount of funding available for expanding plantations and no incentive to be certified. Plantations grow primarily gmelina (Gmelina arborea) which is sold locally and teak (Tectona grandis) (Figure 1) which is shipped to Europe and Southeast Asia.
In both countries, furniture constitutes a large portion of wood products production. Because the majority of hardwoods used in furniture production are reddish to dark brown in color, black cherry (Prunus serotina) and black walnut (Juglans nigra) from the Appalachian region may substitute for the species currently used. Many of the companies interviewed import a variety of building materials from Canada and Chile, including: plywood, osb, mdf, and softwood lumber. Some companies buy southern yellow pine from brokers in the United States. Many of the companies were concerned about the specific dimensions of softwood lumber available from the United States. Most lumber is bought and sold in “varas” (32.9”). The interviewees stated they would prefer lumber from the United States in metric dimensions.
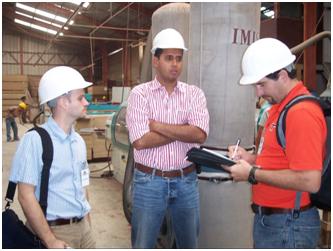
Hardwood and softwood lumber is primarily purchased as “green” and the companies have a lack of information regarding kiln drying. The researchers visited a local cooperative group in El Salvador that recently purchased a Finnish kiln by using funds from a NGO from Finland. Small and medium enterprises use the kiln for drying local lumber.
Logistics for importing did not seem to be a problem in Guatemala. The main port of entry in Guatemala is Puerto Barrios on the Caribbean Coast. The Appalachian region may have a problem importing directly to El Salvador. Most imports to El Salvador arrive by ship to either Guatemala or Puerto Cortes, Honduras and trucked to El Salvador.
There appears to be a large demand for wood from international sources with abundant raw materials and efficient transportation systems to deliver products. Because the Appalachian forest products industry offers products that are similar to those currently imported in Guatemala and El Salvador, they have a unique opportunity to expand their markets into Central America. This marketing research project is funded by the UDSA Federal State Marketing Improvement Program (FSMIP).