By Paula Fallas, dfpaula@vt.edu
There is vast amount of research and information available on Lean Thinking; a management approach that incorporates a series of principals and practices to decrease waste (Czabke, Hansen, & Doolem, 2008). Key aspects for successful implementation of Lean Thinking are top management involvement and support and employee training.
Lean Thinking is not vastly applied to the forest products industry even though companies in this industry are aware of the methodology. In a survey conducted in 2010 targeting primary and secondary wood products industries Virginia findings showed that the majority of industries surveyed were aware of lean (72%) and that a lesser fraction (42%) had implemented lean initiatives (C. F. Fricke & Buehlmann, 2012). There are significant internal and external factors impacting the competitiveness of the US forest products industry such as foreign competition and higher production costs but Lean thinking could be a good strategy to overcome the lack of competitiveness of the US forest products (Czabke et al., 2008).
Implementing lean and sustaining lean is not easy (C. Fricke & Buehlmann, 2012) as it is reflected in the US Forest Products industry. The low implementation rates of Lean Thinking in the US forest products industry could translate to missing opportunities to mitigate risk from competition and to generate competitive advantages (Espinoza, Smith, Lyon, Quesada-Pineda, & Bond, 2012). According to Czabke et al. (2008), a successful implementation of lean thinking can be reached if all employees are well aligned with the lean strategy.
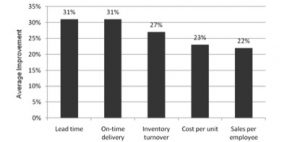
A key aspect in Lean Thinking implementation is to invest in people, recognizing that an educated workforce could achieve higher productivity and innovation levels (Watson, Galwey, O’Connell, & Russell, 2009). Another aspect that is very relevant when implementing Lean Thinking is to gain the support and engagement of the management (Chappell, 2002). This especially important when obstacles and difficulties arise in the implementation processes as only the determination of the managers could steer the organization towards success (C. F. Fricke & Buehlmann, 2012).
Training and education on Lean Thinking can also help to overcome challenging aspects such as resistance to change as well as communication. “Communicating, understanding, and believing in the new vision proved to be difficult, not only for employees, but also for management” (Czabke et al., 2008). The resistance of the US forest products industry towards lean can be explained by the fact that small companies tend to be reluctant towards new business trends because of the lack of funds and that they are more prone to short term planning rather then long-term planning (Westhead & Storey, 2006).
An additional important finding of the survey by Fricke & Buehlmann, (2012) showed that companies employing a Lean Manager show significant difference from the companies that don’t have one since companies with a Lean manager had a higher knowledge and resources to implement Lean. Another way that the industry can increase the success rate of lean implementation is from collaboration with universities. A related success story is Airline Manufacturing, a company that produced solid wood and plywood components. Through a change in the company’s management it was decided to collaborate with Mississippi State University and through an extension specialist the company received consultancy that helped them implement lean and even help them develop a warehouse program to track inventory (Forth, 2004). Through lean this company reduced from 5 million board feet on hand of hardwood lumber to 1 million along with achieving a reduced lead-time. Other success stories of collaboration between the industry and universities show that the industry in general was able to improve lead-time, on-time deliver, inventory turnover, and cost per unit (C. F. Fricke & Buehlmann, 2012).
In summary, the following strategies are recognized as critical steps to a successful lean thinking implementation in the US forest products industries
- Hiring of a Lean manager. The Lean manager should lead the effort and along with the management and employees, the organization needs to enter into a continuous improvement process.
- Invest in training and education of all organization’s employees. Most important asset of any organization it is its people
- The top management must commit and engage with the lean thinking implementation
- Pursue collaborations with Universities. There are a large number of support programs to industry including training, internships, and specific applied research projects.
Bibliography
- Chappell, L. (2002). Womack: Lean thinking starts with CEO. Automotive News.
- Czabke, J., Hansen, E., & Doolem, T. (2008). A multisite field study of lean thinking in U . S . and German secondary wood products manufacture.
- Espinoza, O., Smith, R., Lyon, S., Quesada-Pineda, H., & Bond, B. H. (2012). Educational Needs of the Forest Products Industry in Minnesota and Virginia in 2012. Forest Products Journal, 62(7), 613–622. Retrieved from http://login.ezproxy.lib.vt.edu/login?url=http://search.proquest.com.ezproxy.lib.vt.edu/docview/1433069442?accountid=14826
- Forth, K. D. (2004). Component Supplier Sucessful with lean methods. FDM, 79(9), 36.
- Fricke, C., & Buehlmann, U. (2012). Lean and Virginia’s wood Industry-Part II: Results and Need for Support. BioResources, 7(4), 5094–5108.
- Fricke, C. F., & Buehlmann, U. (2012). Lean and Virginia’s wood industry – Part II: Results and need for support. BioResources, 7(4), 5094–5108.
- Watson, D., Galwey, P., O’Connell, J., & Russell, H. (2009). The changing Workplace : A survey of Employers’ Views and Experiences. Employers The National Workplace Surveys 2009, 1.
- Westhead, P., & Storey, D. (2006). Management training and small firm performance: Why is the link so weak? International Small Business Journal, 14(4), 13–24.