Cellulosic biofuel for transportation and energy is a renewable pathway to cleaner fuels and ultimately to independence from global fossil fuels. This pathway is becoming more focused, but with increasing obstacles like: government regulations, supply shortages, and commercial scaling of technology. Thus, leading many companies to search for funding and stakeholder control of technology, the “valley of death (Alexander and Gordon 2009)” for many evolving companies striving to achieve profitable results as fast as possible. Since 2007, 60 biofuel projects have been developed and are currently in one of the three phases of commercialization, below in figure 1. Of those projects only 12% (7) projects have been able to move into late stage commercialization
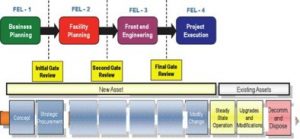
The remaining 88% (53) are in the following stages: 38% (23) are stalled in planning, 35% (13) have been cancelled and (8) shut down, and 15% (9) under construction. Thus, the goal of this research is to gain an in-depth understanding of the causes for the challenges faced by those companies in the cellulosic biofuel industry.
The seven cellulosic biofuel companies in operation currently have a total capital investment of $2.128 billion. Of the seven companies in operation, five technologies have emerged. Additionally, with so many different technologies still in play the small private investors are backing away, even though the quantity and viability of the cellulosic technology is continually being improved. Essentially, the continuing uncertainty of the existing investment risk has pulled the plug on the many financial private outlets willing to lend money.
The added cost of less external investment has left the cellulosic biofuel industry to bolster a considerably larger part of the financial risk, as well as, having to fund aligning themselves within the cellulosic industry and within the biofuel market as a whole to secure the remaining funds.
References
- Alexander, T. (n.d.). K. Lee Gordon – Chadbourne & Parke LLP . Chadbourne & Parke LLP . Retrieved October 18, 2013, from http://www.chadbourne.com/lgordon/
- Brown, T., & Brown, R. (n.d.). A review of cellulosic biofuel commercial scale projects in the United States – Brown – 2013 – Biofuels, Bioproducts and Biorefining – Wiley Online Library. Wiley Online Library. Retrieved October 18, 2013, from http://onlinelibrary.wiley.com/doi/10.1002/bbb.1387/abstract
- The Rise and Fall of Wood-Based Biofuels, Part I | Forisk. (n.d.). Forisk. Retrieved October 18, 2013, from http://www.forisk.com/blog/2013/04/16/the-rise-and-fall-of-wood-based-biofuels-part-i/
- Wesner, B., Designing for sustainability: Begin with the end in mind. Reliable Plant and Lean Manufacturing Journal. Retrieved October 18, 2013, from http://www.reliableplant.com/Read/17421/designing-for-sustainability-begin-with-end-in-mind