This article was published in the October 2010 number of HMR Executive
At the 2010 International Woodworking Fair in Atlanta, Georgia, 27 exporting forest product companies were interviewed about current export markets. The purpose of the survey was to identify export market drivers and barriers of Appalachian forest products. In the past few years, the Appalachian region has suffered from the economic crisis including forest product mill closures and loss of employment due to an increase in global competition. The region needs to increase product competiveness by expanding export markets and improving product promotion (Wang et al. 2010). Exporting of products offers many advantages for firms entering the global market, such as increased profits and credit, market growth, and economic strength (Parhizkar 2008; McMachon and Gottko 1989). Nonexporting companies trying to enter a global market have not primarily because lack of market information regarding product specifications and distribution channels (Ifju and Bush 1993). Overall lack of market information is the main limitation for potential exporters of forest products overseas. A 2002 study of Appalachian hardwood lumber exports (Parsons 2002) showed that a lack of employees and production limitations did not significantly affect exporting, but the need for marketing information was a major hurdle for companies. The companies were asked to identify:
- Top export markets
- Drivers for exporting
- Barriers for exporting
- Primary products and species sold
- Percent of production being exported
The main limitations for the study were the size of companies attending and company representation. Primarily companies interviewed were larger, with more than 100 employees. Also, most of the company representatives interviewed were not directly associated with the company’s export operations, so they may not have been familiar with some of the topics covered in the questions.
Results
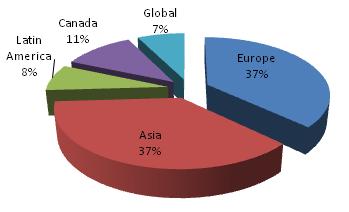
The manufacturers surveyed primarily are located in the Middle Atlantic states including Pennsylvania, Virginia and North Carolina. Most of the brokers that were interviewed had locations in the southeastern U.S. near shipping ports. Currently, forest products companies included in the survey are primarily exporting to Europe and Asia (Figure 1), with some companies exporting to Latin America, Canada or other countries. On average 36% of the production from participants is being exported (Figure 2).
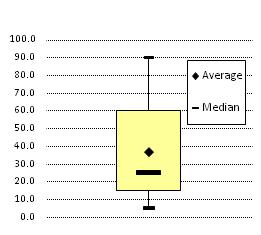
The main products exported to Europe and Asia are Appalachian hardwood lumber and veneer, and also some furniture parts and medium density fiberboard (MDF). Currently the main species exported to Europe and Asia is white oak (Quercus alba) (Figure 3). It was found that veneer companies export a higher percentage (65-90%) of their production than hardwood lumber companies (15-40%). A majority of companies interviewed exported their products through brokers. Companies focused on exporting to Europe and Asia because of business opportunities in the furniture industry and the shrinking of the domestic secondary industry because of the economic downturn. The main barriers affecting exports are custom paperwork, such as phytosanitary documents, and new country regulations (Figure 4). These documents may contain errors or misplaced forms, causing a delay in the arrival of the products to the customer. Companies selling to brokers were not familiar of any trade barriers occurring.
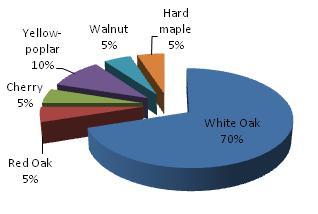
According to the interviewees, a shortage of shipping containers for exporting has been a problem lately. Companies commented that returning containers back to the United States costs more than shipping them from the U.S. This shortage of containers was brought on mainly because of a decrease in container production during the economic downturn of 2008-2009. Also Chinese container manufactures have gone on strike causing an even larger shortage during the peak shipping time from June-October (D’Altorio 2010). Struggling economies in other countries have also deterred companies from exporting to them. A hardwood lumber company stated a lack of continual flow of orders from Latin America has caused them to overlook that region for market opportunities. Also, the time frame it takes to contact the product buyer in Latin America has deterred companies from doing business in that region. One company stated it took over a year to receive an email reply from a Guatemalan company inquiring about a quote. Receiving payments from overseas companies has also affected companies exporting to certain areas. Most forest products companies interviewed require a letter of credit from the customer prior to taking the order. Some companies have encountered problems with language barriers and currency exchange rates when trying to enter a new export market.
Conclusion
The amount of production exported overseas depends on the markets available for products and species. The inconvenience of customs paperwork and the unavailability of containers is the main barrier affecting the amount of U.S. forest products exported. Also it was found that Latin America has been overlooked for market opportunities in part because of the culture differences and past struggling economies. The need to build relationships is critical in these countries to foster partnerships and increase trade with this region.
References
- D’Altorio, T. 2010. The Global Shipping Container Shortage: Riding The Waves To Profits.Invest ment U Research. June 30.
- McMahon, R.O. and J. Gottko. 1989. Export marketing activities of small-firm lumber manufacturers. Oregon State University, College of Business and College of Forestry,Studies in Management and Accounting for the Forest Products Industry, Monograph no. 31.
- Parhizkar, O. 2008. Identifying Impact Factors on Successful Exporting of the United States Hardwood Industries to Mexico, Asia, and Europe. Doctoral Dissertation. Virginia Tech, Blacksburg, VA.
- Parsons, B.A. 2002. An Examination of Appalachian Forest Products Exports. Masters of Science Thesis. Virginia Tech, Blacksburg, VA